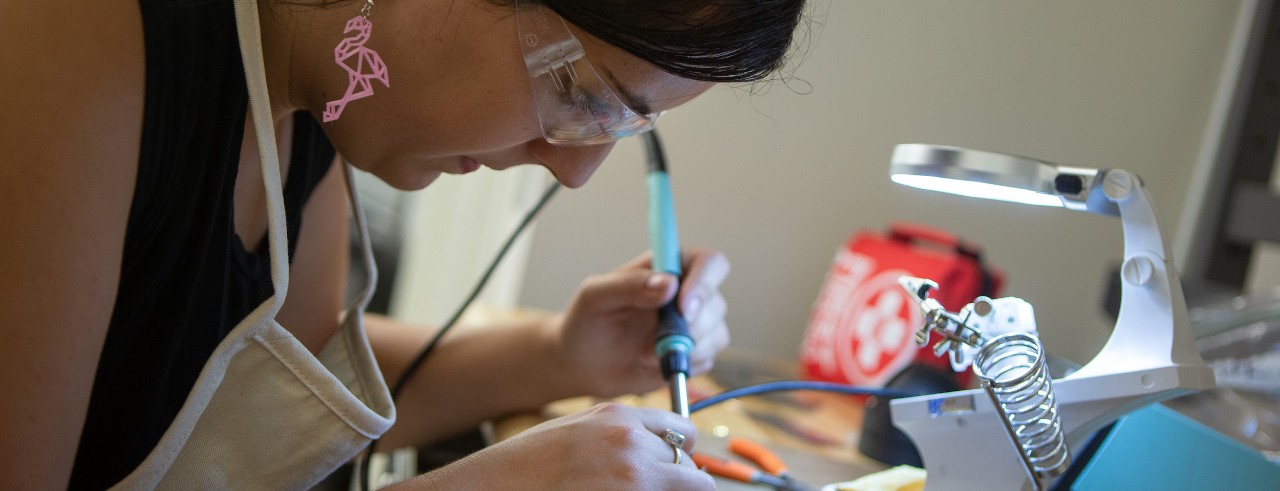
UC’s fashion program gets an innovative makeover
With the opening of the UC Fashion Technology Center and a redeveloped curriculum, UC’s School of Design looks to the future of fashion
Designers are a bit like fortune-tellers. They must predict what consumers will want — known as trend forecasting — while constantly reinventing the dynamics of familiar items from product packaging to pants. And while they don’t have crystal balls to peer into the future, the University of Cincinnati is preparing design students with the tools to do just that.
Innovation is a major priority at UC. As one of the pillars of the university’s strategic direction, Next Lives Here, the push for cutting-edge concepts can be seen in classrooms, UC’s 1819 Innovation Hub, co-op opportunities and beyond. While the strategy is often associated with STEM subjects, UC’s College of Design, Architecture, Art, and Planning is working to incorporate innovation into fashion design with the opening of the Fashion Technology Center (FTC) and a reinvigorated curriculum centered on technology, sustainability and emergent trends.
Located across three spaces on DAAP’s sixth floor, the new center features labs dedicated to “wearable futures” and computer-aided design, textile innovation and apparel production. While use of FTC is now being implemented into the fashion design program, the technologies can benefit many students in various disciplines in DAAP and across UC. Essentially, fashion is something that connects everyone, according to Ashley Kubley, assistant professor of fashion design and head of the FTC.
“When you think about it, clothing is the most ubiquitous thing that we have,” Kubley says. “There's barely any time of the day when we aren't in direct contact with clothing. We are also always connected to technology. It seems only right that two of the things we value most should integrate seamlessly.”
Put those two together and you’ve got the emergent field of wearable tech. Kubley’s definition of wearable technology is something portable and carried on the body that aids a person’s performance. Today that’s represented by smartwatches and activity trackers, but soon, she says, we’ll be seeing more electronics embedded in garments as opposed to just stand-alone gadgets.
“Fashion students hold the knowledge of how material works with the body, how to develop patterns and design textiles, which are nontraditional elements for things like computing,” Kubley says. “When you think of smart technology, you might think of your cellphone or Apple Watch or a device that’s not necessarily a soft textile-based product. But now that we’re seeing so much more opportunity for the integration of technology into those materials in interesting new ways, you really have to have a fashion designer on your team who understands the materiality and function of clothing.”
Assistant Professor of Fashion Design and head of DAAP's Fashion Technology Center Ashley Kubley leads a tour of the FTC at its recent opening. Photo/Andrew Higley/UC Creative Services
In the FTC’s Wearable Futures Lab, students can create smart garments by using conductive threads or embedding LED lights, circuits and sensors that could monitor anything from posture to heart rate or could sense dehydration — the potential is endless. And while a “smart textile” could be as simple as an input/output — think a light that blinks at the rate of your heartbeat — Kubley says they’re challenging students to think even farther.
“What we really want to push is for these to be active, super-smart textiles that can not only sense something, but learn to react to it,” she says. This could look like a material that changes color when it senses air pollution or yoga pants that alert the user when their body is out of alignment. “There’s thousands of applications for it,” Kubley says.
The lab also boasts computer-aided design software from the industry-leading fashion tech company Lectra, used by brands from Abercrombie & Fitch (UC fashion design’s biggest co-op employer) to Louis Vuitton. Traditionally when prototyping a garment, a designer would draft a pattern on paper, trace the pattern on fabric, cut that out, then construct and fit the garment on a model. Using industry standard software like EFI Optitex and CLO, that process can be done digitally, with a 2D pattern and a 3D avatar specific to any shape or size. Designers can see what a garment will look like and how it will fit the body and make virtual changes to it before they even make a physical sample, saving time and resources.
“It’s a push toward not only making things more quickly — so it caters toward the fast-fashion market — but it also caters to the sustainable design market because it reduces the amount of waste that you have to use in prototyping,” Kubley explains.
Recent grad Layne Rumpke embeds wearable technology in a sweater for her senior capstone project, titled "Sentiment."
Sentiment utilizes wearable technology and social media to aid connection between users, their clothing and their peers.
Technologies such as digital patternmaking and virtual fitting will inevitably change the consumer’s experience as well.
“In my opinion,” Kubley says, “the future will be all about inclusive design and the customer having a very active role in the design and development of customized products.”
She predicts that body-scanning technology and on-the-spot production will change the brick-and-mortar shopping experience: Customers could go into a store and get a full-body scan measuring more than 1,000 parameters of their body. A digital pattern based on those measurements can be fit on a one-of-a-kind avatar and the customer can see exactly what the garment will look like on them in real time. Once approved, the design is printed digitally, laser-cut and sewn together and delivered to the customer.
Imagine never again having to walk into a fitting room with a stack of clothes, unsure anything will actually fit. Or getting custom, one-of-a-kind clothing every time you shop that fits even better than tailored clothing. Soon, the FTC hopes to have its own 3D body scanner.
In another FTC space, the Textile Innovation Lab offers a variety of equipment that students can use to develop their own materials for the garments they're designing, including 3D printers, a digital fabric printer and automated knitting, embroidery and weaving machines.
Students have access to digital patternmaking and virtual fitting technologies used by industry leaders. Photo/Andrew Higley/UC Creative Services
Another component of FTC, the Natalie Altieri Apparel Production Lab, is a high-tech sewing studio. Hosting advanced, specialized apparel construction equipment, including an ultrasonic welding machine and industrial-grade equipment that can sew leather goods, here students can produce production-level samples. The lab is named in honor of a fashion design student who passed away in 2015.
Kubley hopes these new spaces and tools inspire even more interdisciplinary work between fashion students and industrial and communication designers, engineers and others. She’s already working with UC’s College of Engineering and Applied Science on a project involving smart nanotube textiles and is working with UC’s 1819 Innovation Hub’s commercialization incubator.
“It’s beneficial to have these two different kinds of brains in the room together,” she says, “and those collaborations have been really dynamic. We are disrupting the way that researchers have traditionally worked in their own silos.”
When planning the new vision for the fashion design program, Endowed Chair and Director of DAAP's Myron E. Ullman, Jr. School of Design Gjoko Muratovski looked back at the school's history for inspiration.
"Our design school was established with a clear mandate to drive innovation for industry, and Cincinnati is a city with strong manufacturing heritage and a tradition of making," he says. "From the very beginning we had a study program that specialized in textiles design and have worked closely with industry on creating new ideas and capabilities. Now is the time for us to introduce the next stage of our development. With the industry-grade equipment in the new Fashion Technology Center we can now operate on a very advanced level. More importantly, the new capabilities that we have created allow us to push the boundaries further and drive innovation on a level that sometimes even our industry partners can not deliver on their own.”
The world is taking notice. DAAP was named one of the Best Fashion Schools in the World 2019 by website Business of Fashion. This year Tessa Clark, a 2010 graduate, became DAAP’s third alumna to compete on the fashion design reality competition “Project Runway,” coming in fifth place while building her sustainable luxury brand Grind and Glaze here in Cincinnati. Fellow fashion alum Hannah Beachler made history at this year’s Academy Awards as the first black person to win a production design Oscar for her work on “Black Panther.”
“Fashion students from UC will be able to imagine the future of wearable technology. Not only are they are already equipped with the skills to predict what consumers will want, they are now able to prototype and test those concepts using the resources that the new FTC provides. Those skills will give them a critical edge in the fast-moving professional world of fashion technology.”
Featured image at top: A fashion design student uses soldering equipment in the Fashion Technology Center. Photo/Andrew Higley/UC Creative Services
Learn more about DAAP fashion design
- Read about the fashion design program in DAAP’s renowned Myron E. Ullman Jr. School of Design.
- Watch the video from this year’s DAAP Fashion Show.
- Schedule a visit to DAAP.
- Apply to UC.
- Follow DAAP’s Fashion Technology Center on Instagram: @daap_FTC
Related Stories
University of Cincinnati celebrates DAAP's class of 2024:...
April 27, 2024
Discover the achievements of the University of Cincinnati's College of Design, Architecture, Art, and Planning's Class of 2024 as they graduate into the alumni family, showcasing exceptional talent and innovation. From prestigious awards to prominent job offers, these graduates exemplify the transformative power of creativity and dedication in shaping tomorrow's leaders.
Ancient Maya blessed their ballcourts
April 26, 2024
Using environmental DNA analysis, researchers identified a collection of plants used in ceremonial rituals in the ancient Maya city of Yaxnohcah. The plants, known for their religious associations and medicinal properties, were discovered beneath a plaza floor upon which a ballcourt was built, suggesting the building might have been blessed or consecrated during construction.
UC celebrates record graduating class at commencement
April 26, 2024
UC celebrated its doctoral hooding and master's recognition ceremony at Fifth Third Arena as part of its three-day commencement for the largest graduating class in university history.