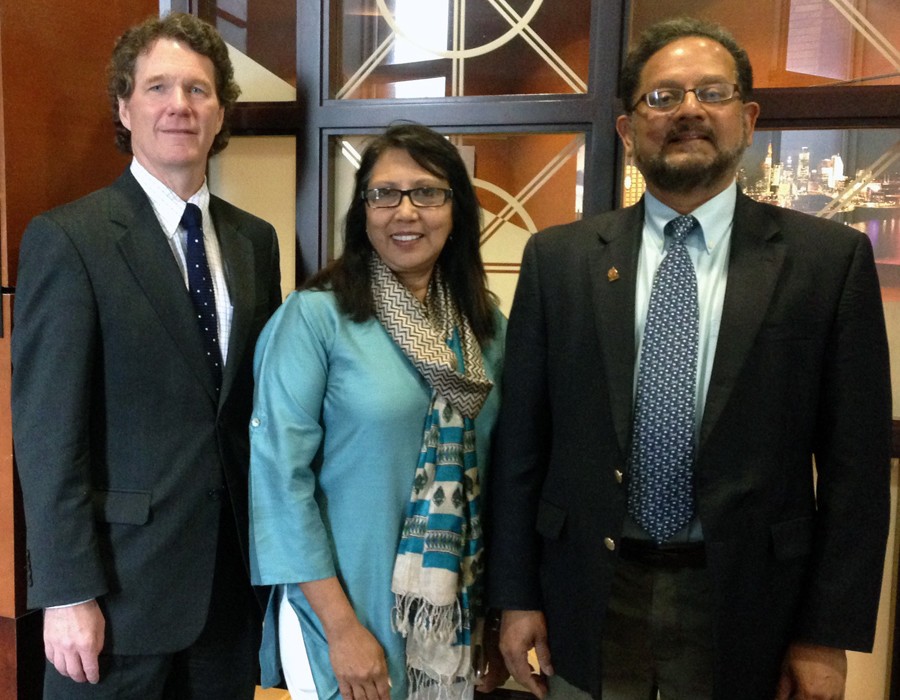
UC Cancer Institute, Lindner College Partner for Patient Satisfaction
While patient care is mostly about the delivery of treatment with the overall goal of wellness and an improved quality of life, there is a business aspect that cannot be ignoredand when it is, oftentimes patient satisfaction and efficiency deteriorate, making the overall goal unreachable.
Seeing gaps in this is what led Franklin Smith, MD, clinical director for the University of Cincinnati Cancer Institute and pediatric oncologist specializing in hematologic malignancies, or blood cancers, to seek a solution for cancer care within the institute.
"I saw major problems and a need for Lean training among faculty and staff, he says.
Lean involves a set of practices that originated in the business world and are based on the assumption that customer satisfaction is achieved by identifying and eliminating or reducing all activities that do not create value for the end-customer. These practices were first organized by Toyota into a management philosophy called the Toyota Production System, but they have been used successfully to drive customer satisfaction initiatives in financial services, banking and health care.
"Its about customeror in this case patientsatisfaction, Smith says. "In 2011, UC Health didnt have the resources necessary to monitor and correct certain aspects of cancer clinical care from the operations stand point. I went to Vice President and Chief Operating Officer Nancy Barone with this, and she suggested that I get in touch with Rajan Kamath, PhD, from the UC College of Business.
Kamath, associate professor of strategy and international business with the department of management at the Carl H. Lindner College of Business, who has published award-winning Lean research in the Harvard Business Review, had just created a class about the use of Lean practices in health care for graduate students at UC.
"With the Lean model, the two main goals are customer satisfaction and process analysis to improve both efficiency and effectiveness. Health care is the most recent context for the application with these cross disciplinary needs, leading to the creation of a new class for MBA students about strategy titled, Lean Strategies in Health Care Management, he says. "However, we needed to give them a final project, and with this partnership, we could do that while providing real-life experience in a cancer-related health care setting.
For four semesters, student teams have spent 10 weeks immersed in the use of Lean to analyze a problem previously identified by Smith and present UC Cancer Institute leadership with a recommended solution at the end of the semester.
"This is fact-based, third-party analysis with focus placed on the root cause of the problems and applications needed to fix them, says Kamath.
And its win-win, adds Smith.
"Were finding solutions to real clinical problems at no cost to our health care system, and these students are getting real-world experience that helps them gain jobs after graduation; students from this program have a 100 percent placement rate following completion of the program, he says.
Deepa Bobbili, who completed the course in the 2013 spring semester, says the team focused on improving the use of electronic health record systems at a rapid pace to help with timely delivery of chemotherapeutic products to outpatient clinics with the goal of gaining accreditation by Institute for Safe Medication Practices standards.
"Most health care professionals are too busy or not trained to think about improving processes, Bobbili says. "As I progressed through the masters program in business administration coupled with a graduate certificate in data analytics, I was introduced to the Lean Healthcare Six Sigma elective, which thrilled me, as I was looking to learn to be as productive and effective as I could if applying Lean to daily project work.
"I enrolled for the course, and during our first kickoff session, I found out how Lean application has been addressing operational and administration issues by using departments and people dedicated to quality improvement. I realized Lean is unique because although it was a systematic and proven method, it also had the authority and infrastructure to sustain real change.
Additionally, Bobbili, who now is employed as a senior project manager and implementation lead at Altruista Health, says the course helped in gaining knowledge and insight in forming a strong argument for a Lean-based health care system and in understanding the "nitty gritty of established quality-management tools.
Smith says that all the projects completed during the course have solutions that are being implemented. One recent project involves the creation of a system to ensure that patients have the opportunity to preserve their ability to have children after completion of their cancer therapy and another focuses on the reorganization of processes to help speed up the start of inpatient chemotherapy.
"Most of the changes are centered on communication and culture changedoing things differently for a better result, says Ratee Apana, PhD, associate professor of business who is also involved in the partnership. "Its less about what people are doing wrong and more about changes in processes to enhance the results.
"There are also mentorship opportunities available for former students. It really follows a multidisciplinary approach and allows people to think laterally.
Smith adds that the hope is to carry this partnership into other areas of the College of Medicine as well as the other health colleges at the Academic Health Center, including allied health, pharmacy and nursing.
"With this meeting of resources, students are getting the best training possible and patients are getting better care, he says.
Tags
Related Stories
Is ketamine the answer to treatment-resistant depression?
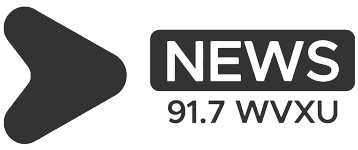
May 16, 2024
The University of Cincinnati's Stephen Rush joined WVXU's Cincinnati Edition to discuss the use of ketamine and esketamine to treat treatment-resistant depression.
UC study: Severe ischemic strokes rare in total patient...
May 15, 2024
The University of Cincinnati’s Yasmin Aziz will present research at the European Stroke Organisation Conference that found severe ischemic strokes with the most severe damage are rare in the total stroke patient population.
Increasing syphilis cases highlight treatment barriers across...
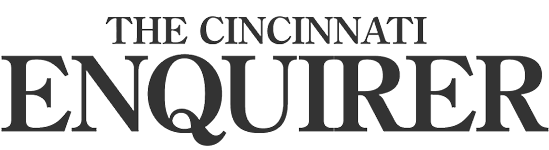
May 14, 2024
The University of Cincinnati's Carl Fichtenbaum spoke with the Cincinnati Enquirer about a recent report that found Hamilton County syphilis cases reached a six-year high in 2023.